Delivering a new airplane to a customer at our Faria Lima facility is usually a routine event. We´ve done it Iiterally thousands of times! But with the ongoing effects of the pandemic here in Brazil, we’ve had to adopt smart technology – including drones and live camera transmissions – to ensure the aircraft is delivered on time.
We started testing the new processes in June and, so far, the feedback has been really positive. We’ve been working really closely with our partners and customers and everyone is extremely satisfied with the modified procedures considering the extraordinary circumstances. [Learn more]
Nothing compares to sitting side-by-side with our customers in the cockpit and cabin, checking components, getting immediate feedback, walking around the airplane, pointing, touching things, demonstrating functionalities, and riding together on the test flights. But new physical distancing rules prevent us from conducting those ordinary tasks jointly as we did before. Yet, deliveries continue right on schedule.
We have, of course, implemented strict on-site health protocols for the safety of our customers and the inspection teams. Visitors to the factory receive personal hygiene kits, have daily temperature checks, and travel in clean, secure vehicles. Their offices are continually sanitized during the day as are our buildings, hangars, and equipment. Everyone must wear a mask.
Inspecting an airplane requires many people working in close proximity to each other. Under the new distancing rules, it’s not possible to have, for example, four people in a cockpit, or several technicians making adjustments in the cabin at the same time. We’ve had to re-engineer the way we perform these everyday tasks.
Here are some of the high-tech and low-tech ways we’ve made the delivery process as seamless and contactless as possible.
On the Ground
– daily e-briefings/e-meetings – we’ve increased the number of online meetings compared to before the pandemic and now conduct them via local and international video conferencing.
– document exchanges – continue to be 100% digital.
– loose items – transferred via sterile pouch; receipt confirmed by digital photos.
On the Aircraft
– exterior inspection – via drone videos and pictures.
– interior inspection – live camera transmission of cockpit/cabin checks.
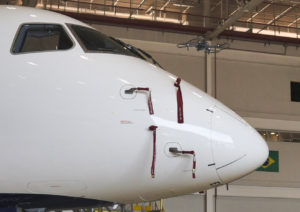
During the Test & Acceptance Flights
-Cockpit and flight filming – details of the cabin and aircraft exterior are sent to the customer for review.
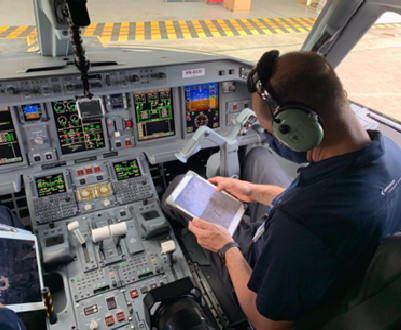
We know that our customers may not be able to send their usual staff contingent for a delivery. However, we can complete our check lists with hands-on and new digital methods. In fact, smart technology allows customers to share the aircraft inspection process in real time with their own technical personnel back in their home country.
I’m incredibly proud of the work our teams have done to keep the delivery process smooth and efficient. It was no easy task and I commend them for doing it so quickly in light of such a stressful environment. Even though we’ve had to adapt to this new way of working, I’m looking forward to returning to the day when I can once again personally shake the hands of all our visiting customers before they board their new E-Jet for the flight home.
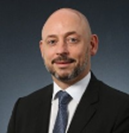
Simon Newitt
Vice President, Contracts & Asset Management
Embraer Commercial Aviation